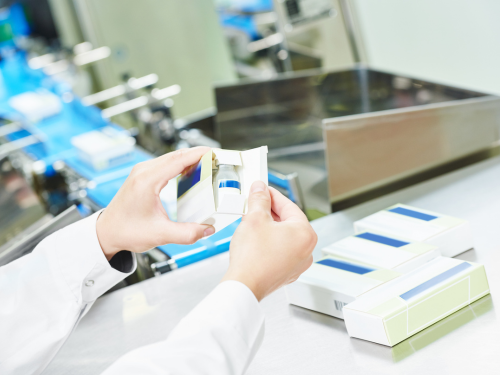
In the dynamic landscape of pharmaceuticals and medical devices, regulatory compliance stands as a cornerstone of patient safety and well-being. Yet, ensuring compliance with evolving standards and regulations poses significant challenges for organizations worldwide. Traditional methods of producing Instructions For Use (IFUs) and Patient Information Leaflets (PILs) have often proven inadequate in meeting these demands.
These documents serve as crucial sources of information for patients, providing guidance on the proper use of medical devices and medications. Inaccuracies or errors in these leaflets can have severe consequences. When it comes to pharmaceutical and medical device labeling, the risks can even be life threatening.
Therefore, ensuring the accuracy and compliance of patient information and instructions for use leaflets is essential for safeguarding patient health and maintaining regulatory adherence. However, with the introduction of automation in the labeling and artwork industry, a new era of efficiency, compliance and accuracy has arrived in IFU production.
Bob Tilling, our label and artwork expert, sheds light on the transformative power of automation in IFU production. Let's discuss some of the insights Bob has shared:
Addressing Regulatory Gaps
Having anything from 100 to over 1,000 IFUs is not uncommon for a mid-sized device manufacturer. Re-writing in a style appropriate for the user, the addition of new symbology and statements, plus translation into 20+ EU languages is making the task of updating these to comply with the new EU Medical Device Regulation (EU MDR) much larger than first anticipated for many device companies.
The new EU MDR is significantly longer than the EU Medical Devices Directive (MDD) and will require most medical device manufacturers to update their clinical data, technical documentation and labeling which includes the leaflets.
Non-compliance with EU MDR labeling requirements not only puts patients at risk but also exposes organizations to legal repercussions and reputational damage. Therefore, ensuring the accuracy and compliance of patient information and instructions for use leaflets is essential for safeguarding patient health and maintaining regulatory adherence.
Many organizations recently have found themselves in a quandary, as traditional systems, including Product Lifecycle Management (PLM) systems, often fall short in controlling layout and content. Veraciti emerges as a beacon of hope, offering a comprehensive solution that not only manages content but also controls layout, ensuring compliance with regulatory standards.
Streamlining Processes, Eliminating Errors
The traditional approach to IFU production often involves a laborious process that involves input from several stakeholders across the globe. This decentralized approach not only consumes time but also increases the risk of errors. By using an automated enterprise labeling software, such as Kallik’s Veraciti, you can revolutionize this process by automating the generation of the leaflet from a pre-approved single source of truth with pre-approved, automatic translations available too, eliminating the need for manual intervention when creating and updating the leaflets.
Breaking Language Barriers, Ensuring Consistency
When it comes to IFU leaflets, it’s crucial that the information can be correctly understood by patients and healthcare professionals all over the world. Veraciti revolutionizes this process by enabling organizations to swiftly generate IFUs in multiple languages, all within a matter of seconds. This groundbreaking capability eliminates the necessity for linguistic expertise, a significant obstacle particularly for non-native speakers who may struggle with language nuances.
Unlike competitors who rely on less accurate methods like Google Translate, Veraciti offers pre-approved translations derived from a single source of truth, ensuring consistency and accuracy across all IFUs. This not only streamlines the process but also reduces the workload, as organizations no longer need to create separate IFUs for each language, enhancing accessibility. The ability to swiftly generate accurate translations is a game-changer, empowering non-native speakers to access vital medical information with ease and confidence, ultimately contributing to improved healthcare outcomes on a global scale.
Making the Move to eIFUs (Electronic IFU)
In today's fast-paced digital world, the transition from traditional paper-based IFUs to electronic formats marks a significant leap forward in efficiency and accessibility. Electronic IFU leaflets offer a long list of benefits, including streamlined access, enhanced user experience, the ability to deliver multilingual content seamlessly and not to mention the sustainability benefits. Furthermore, when regulations are updated and the information required on IFUs changes with them, this then can mean that organizations need to change thousands of labels to stay compliant. With electronic IFUs, the process is far less time consuming and involves far less waste. As Peter Muller explains in Med-Tech Intelligence: “Paper-based IFUs/PILs are printed in bulk leading to waste when product/manufacturing information or safety advice needs to be updated. There may also be a level of risk to patients if they are accessing information that has been superseded.”
With this rising demand for electronic IFUs, organizations are increasingly turning to automation. Unlike traditional methods that rely on manual processes and paper-based documentation, Veraciti empowers organizations to generate IFUs in electronic formats, including XML files. This capability not only ensures compliance with regulatory standards but also opens up a world of possibilities in terms of accessibility and integration. With Veraciti, organizations can create IFUs that can be downloaded as XML files, enabling seamless integration into websites and digital platforms. By harnessing the power of automation and electronic IFUs, organizations can navigate the complexities of regulatory compliance with ease while delivering an unparalleled user experience to their customers.
Case Study: Empowering Össur With Greater Control
Our collaboration with Össur, a leading provider of Class II medical devices, exemplifies the transformative impact of automation in IFU production. Össur faced numerous challenges, including disparate legacy systems, delays in product launches, and limited control over IFU assets. With the implementation of Veraciti, Össur achieved remarkable results, consolidating IFU phrases into a centralized system, enhancing visibility, and streamlining the approval process. The ability to pre-approve phrases and standardize IFUs has not only improved efficiency but also ensured compliance with regulatory requirements. You can read more about how we helped Össur here.
Success Story: Keeping People Safe with Cardinal Health
In our collaboration with Cardinal Health, a global leader in healthcare services, we have witnessed firsthand the critical importance of accuracy and compliance in IFU production. By providing solutions that streamline the compliance process and eliminate errors, we have helped Cardinal Health navigate the complexities of regulatory standards, particularly in the context of MDR compliance.
As Bob Tilling aptly puts it, "The ability to pinpoint necessary artwork modifications swiftly and accurately is instrumental in not just compliance but also in ensuring accuracy in crucial elements such as Instructions for Use (IFUs)."
Safeguarding Lives, Ensuring Compliance
Through adopting our approach, creation of multiple language EU MDR compliant 30 page IFUs is down from 3-5 hours to just 30-40 minutes with the time taken to generate individual labels reducing from 1 hour to around 10 minutes. With 350 IFUs and 10,000 labels, 5 person years of lost time has been recovered just for Class III devices alone.
In conclusion, automation in IFU production is a game-changer for compliance, accuracy and efficiency. By leveraging the power of technology, organizations can streamline processes, eliminate errors, and ensure compliance with regulatory standards. Our partnerships with Össur and Cardinal Health underscore our commitment to empowering organizations with complete regulatory confidence.
To read more about the latest EU MDR and the issues with IFUs, read our blog: EU MDR Labeling Compliance - Are We There Yet? Looking for more advice? Speak to one of our experts by emailing enquiries@kallik.com.